
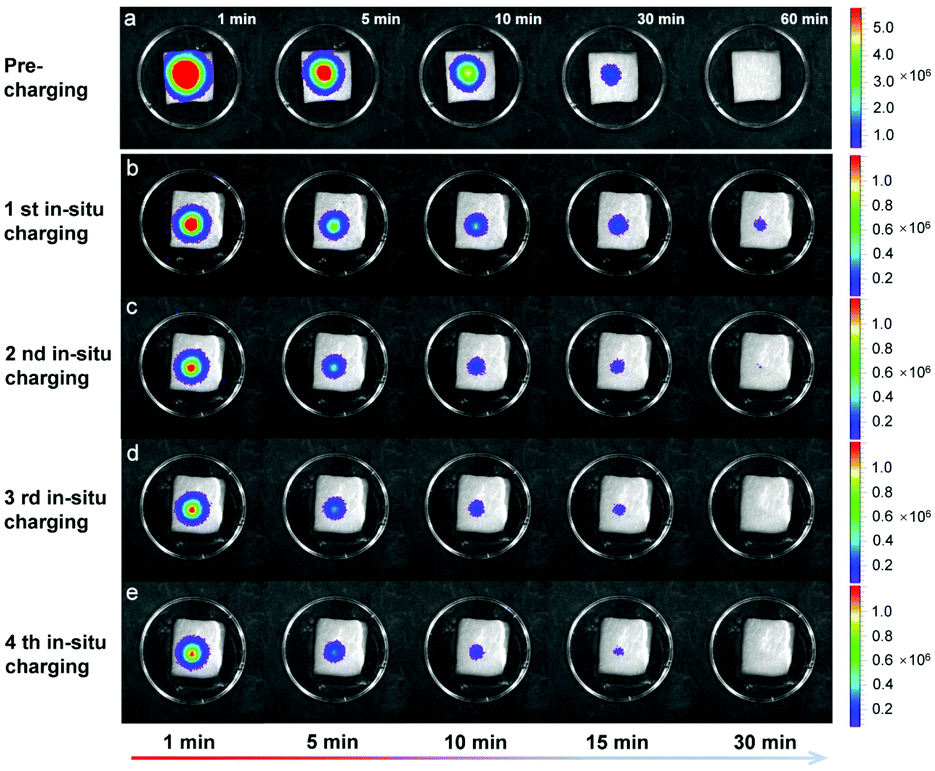
It should be noted that this method does not apply to aerated concrete either autoclaved or normally cured, or lightweight aggregate concrete with an open structure. (4.4)).įor lightweight aggregate concrete, the secant modulus of elasticity may be assumed equal to the value for normal weight aggregate concrete multiplied by ( ρ/2200) 2, where ρ = density of lightweight aggregate concrete between 8 kg/m 3. However, CEB MC 90-99 specifies an expression that allows for different temperatures, and this is given in Chapter 4 (Eq. The estimation of modulus of elasticity applies to concrete cured and stored at a temperature of 20 ☌, and there is no provision in BS EN :2004 for other temperatures.
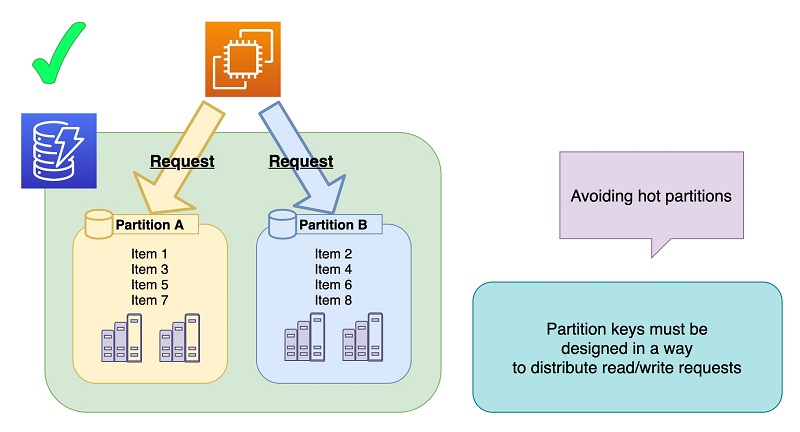
On the other hand, for basalt aggregates, the value should be increased by 20%. For concrete made with limestone and sandstone aggregates, the modulus of elasticity should be reduced by 10% and 30%, respectively. As stated in Chapter 4, the secant modulus of elasticity applies to normal weight aggregate concretes made with quartzite aggregates. Relationships for modulus of elasticity in terms of characteristic strengths are given in Table 4.1. Where f c28 = 28-day mean cylinder compressive strength (MPa). When a less accurate estimate is considered satisfactory, 70-year values of creep coefficient may be estimated from Figure 11.3 where values are valid for temperatures between −40 ☌ and +40 ☌, and a mean relative humidity between RH = 40% and 100% the procedure is illustrated in Figure 11.3(c).įor lightweight aggregate concrete, the creep coefficient ϕ 28( t, t o) may be assumed equal to the value for normal weight aggregate concrete multiplied by ( ρ/2200) 2, where ρ = density of lightweight aggregate concrete (kg/m 3). Where t oT = temperature adjusted age that replaces t, T i = temperature (☌) during time period Δ t i, in which the temperature T i prevails and n = number of time intervals considered.īS EN : 2004 does not consider temperature effects during the creep process, although the CEB MC 90-99 specifies relevant expressions as detailed in Chapter 10.Īccording to BS EN, the mean coefficient of variation of ϕ 28( t, t o) deduced from the RILEM data bank is of the order of 20%. These findings are in line with the results reported on the normal Class C fly ash alkali-activated system ( Sathonsaowaphak et al., 2009 Chindaprasirt et al., 2007 Somna et al., 2011 Lee and van Deventer, 2002). Strength development is improved with the increases in sodium silicate content (sodium silicate/NaOH of 0.33–3.0) and curing temperature of 25–60 ☌ with the optimum NaOH concentration of 10 m. Also, the increase in the amount of fine aggregate results in an increase in concrete density due to the higher density of fine recycled lightweight aggregate. The fine aggregate with high surface area offers better bonding between alkali-activated matrix and fine aggregate than that of coarser aggregate, and thus the increase in fine aggregate from 0% to 70% results in concrete with increased strength. The strength slightly increases with the increase in the amount of fine recycled lightweight aggregate content (reduced recycled coarse aggregate) as shown in Figure 19.1.

Crushed waste lightweight concrete block has been used successfully as recycled aggregates for making lightweight alkali-activated concrete using NaOH, sodium silicate and fly ash ( Posi et al., 2013) with acceptable 28-day compressive strength of 1.0–16.0 MPa, density of 860–1400 kg/m 3, water absorption of 10–31%, porosity of 12–34%, and modulus of elasticity of 2.9–9.9 GPa. Crushed lightweight aggregate concrete (LWAC) can also be used as an aggregate in concrete (recycled LWAC-aggregate) ( European Union – Brite EuRam III, 2000).
